Engineering Excellence in Extreme Environments: Rotamec’s Innovative Solution Revolutionises Blast Freezer Maintenance
Rotamec faced a significant challenge at one of our longstanding food processing clients. The task involved working on the Blast Freezers, a demanding job due to the constricted space and extreme conditions, characterised by moisture build-up and freezing temperatures. One of the four ABB motors in the freezer was nearing the end of its life, necessitating a replacement. This process was complicated by the need to remove the impeller shaft and impeller, a labour-intensive task exacerbated by the conditions, posing risks of contamination to the conveyor belt.
Previous Experience:
Rotamec engineers had performed similar tasks multiple times, but each occasion presented unique difficulties, particularly with the shaft cutting process. The post-installation period also required meticulous attention due to the damaged shaft, leading to extended labour and downtime.
Innovative Solution:
After encountering unprecedented challenges in a previous installation, Rotamec engineers were tasked with devising a cost-effective and efficient solution. The breakthrough came with the redesigning of the impeller. The worn-out impellor hub was transported to Rotamec’s Cheddar workshop, where CAD drawings were created for a new design. Critical dimensions were recorded, leading to the fabrication of a new impeller with a taper lock design, tailored to fit the motor drive shaft. This design was developed within a tight 5-day window.
Installation and Results:
The new backward curved impeller was quickly installed by Rotamec’s confined space trained engineers, ensuring minimal downtime. The client was able to maintain production throughout the process, thanks to backup Blast Freezer motors. The new taper hub impeller design significantly eased the fitting and removal process for future changeovers. It also reduced the likelihood of shaft damage, potentially limiting future replacements to just the taper lock bush. This innovation meant reduced labour time for Rotamec engineers and a quicker return to full production capacity for the client.
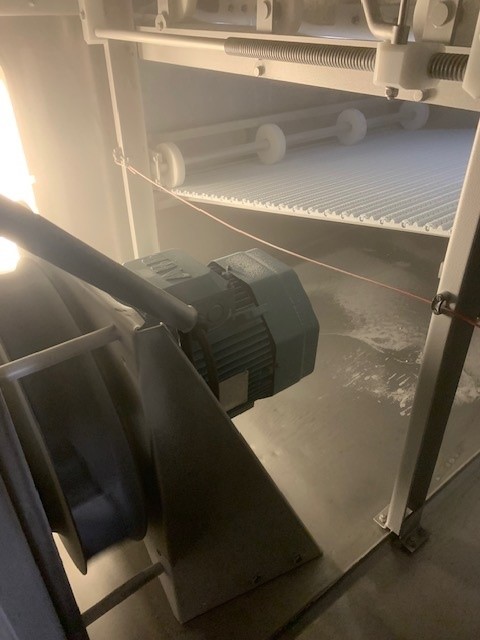
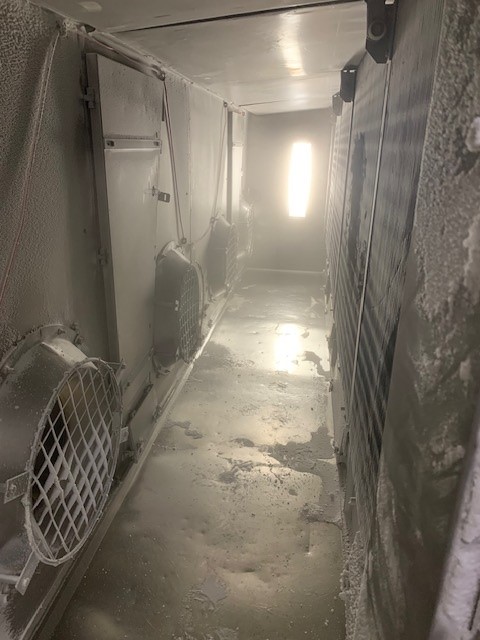
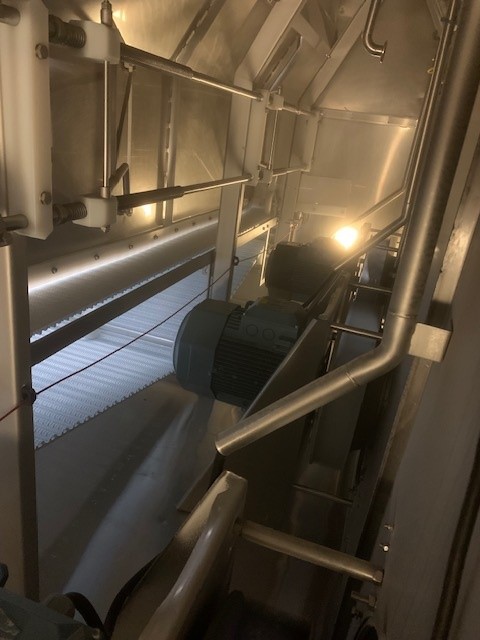
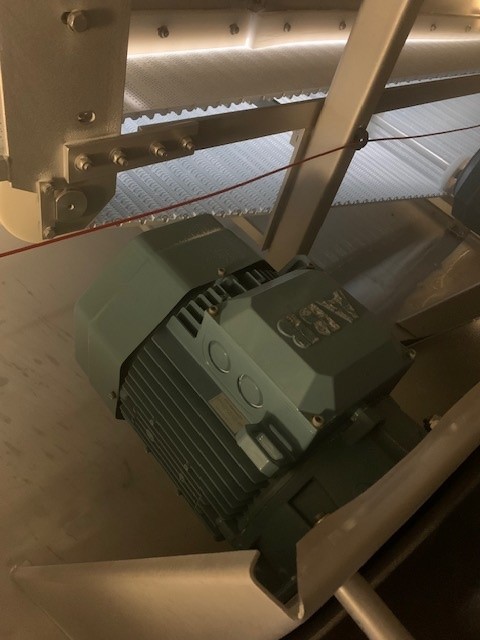