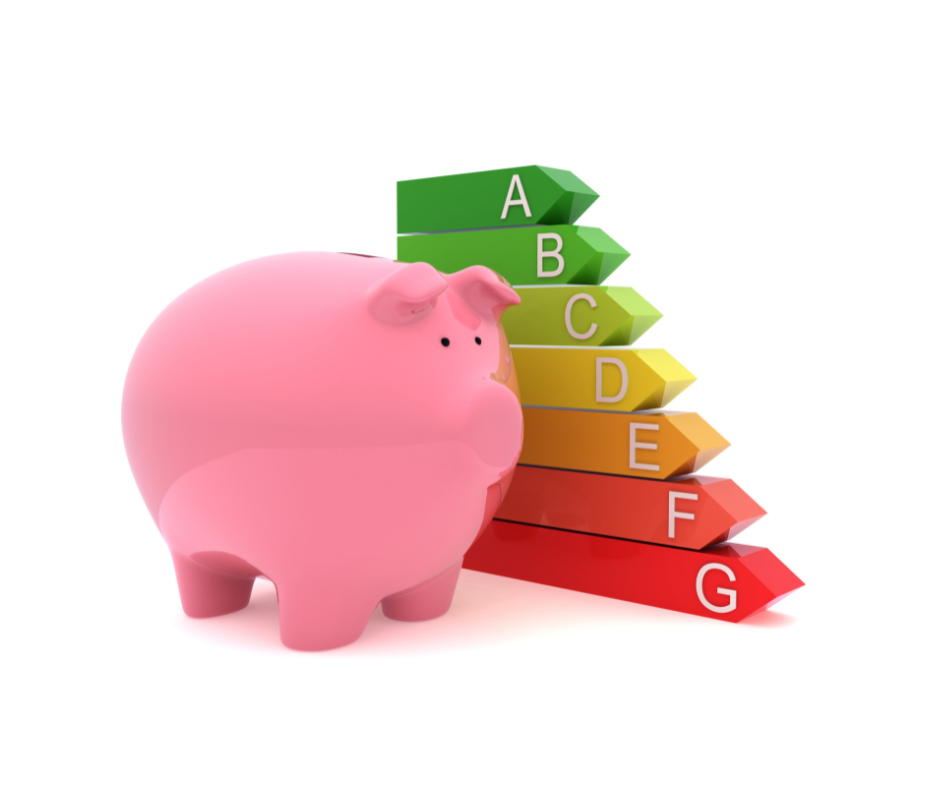
Energy prices have risen dramatically in the past months, forcing businesses to look for ways of improving efficiency. For those who use electric motors, whether to power pumps or machinery, this is acutely the case. Motors typically account for the highest energy cost of any electrically powered device; in fact, the International Energy Agency says electric motors account for more than 40% of global energy consumption.
Motors and energy cost
In the UK, despite the government’s recent energy assistance package with a six-month price fix, reports suggest that businesses will still pay up to . Taking a larger 120kW motor, running 24/7, and energy costs could soar in excess of £200,000 per year.
Despite the need for cost saving, critical applications have to keep running. But, energy efficiency technology is available that can decrease total cost, including the initial investment.
Optimising motor efficiency
Taking the motor itself, its operation is never 100% efficient. Energy losses are mainly a result of electrical resistance in the stator’s copper windings, as well as in the rotor, and core losses in the motor’s steel laminations.
The good news for facilities managers and energy stakeholders is that upgrading to a higher efficiency motor can save significant cost. The International Electrotechnical Commission (IEC) provides classification on the efficiency of motors, ranging from IE (International Efficiency) 1, representing standard efficiency, through to IE4 super premium efficiency.
The performance that determines a motor’s IE classification is based on a scale that factors in frequency, pole count, and kW output, as well as the motor’s duty/working point and percentage efficiency rate. Combining this data with the operational duration and the kW/h charge, it’s possible to calculate a motor’s running cost. We can also use this data to understand how a higher IE-rated motor might compare.
For example, an IE1 type motor at 120 kW input, with 24/7 operation, running for 50 weeks a year, can cost around £70,500 to run, based on a low kW/h charge of 0.07p. Upgrading to an IE3 motor can cut nearly £3,000/year from this cost. Assuming the kW/h price rises to the 0.21p cap, installing an IE3 can save over £8,500, while an IE4 motor can save as much as £10,000-plus.
Some manufacturers, such as ABB and Nord, also now offer an even more efficient ‘IE5 standard’. These motors are typically based on permanent magnet synchronous motor technology, creating a permanent magnetic field that increases efficiency further still. High energy savings are achieved in particular when applications require partial load and speed operation, such as a 50% load at a 37.5% speed.
Energy cost audit
It’s no accident that facilities and plants are increasingly requesting motor energy use audits from our engineers as a result of rising energy costs. Based on your input data, an energy audit can calculate a transparent cost comparison and saving through motor efficiency upgrade.
And, the saving is cumulative: the more motors a plant operates, the more kW consumed, and the greater the cost saving potential.
Reducing energy cost with variable speed drives
An electric motor runs at the maximum frequency and voltage of its supply. This means that the motor operates constantly at full speed, using maximum electricity, but many applications don’t need this continual operation. Even when the effects of motor speed on the application’s output are regulated, for example by using a gearbox or a damper in a fan system, the motor itself will still run at full speed.
Many applications such as those involving fans, pumps, and compressors often fall into this category. When the desired level is reached, such as optimum aeration of sewage or the ideal temperature of an environment, the motor’s frequency can be regulated to reduce energy consumption. This can be achieved by installing a variable speed drive, also known as a variable frequency drive (VSD or VFD), that controls the frequency and voltage supplied to the motor.
The energy saving provided by a variable speed drive depends on the load and operational requirements, but a VSD can automatically control a motor based on changing conditions, reducing speed accordingly. Integrating a VSD, energy savings of up to 40% are possible.
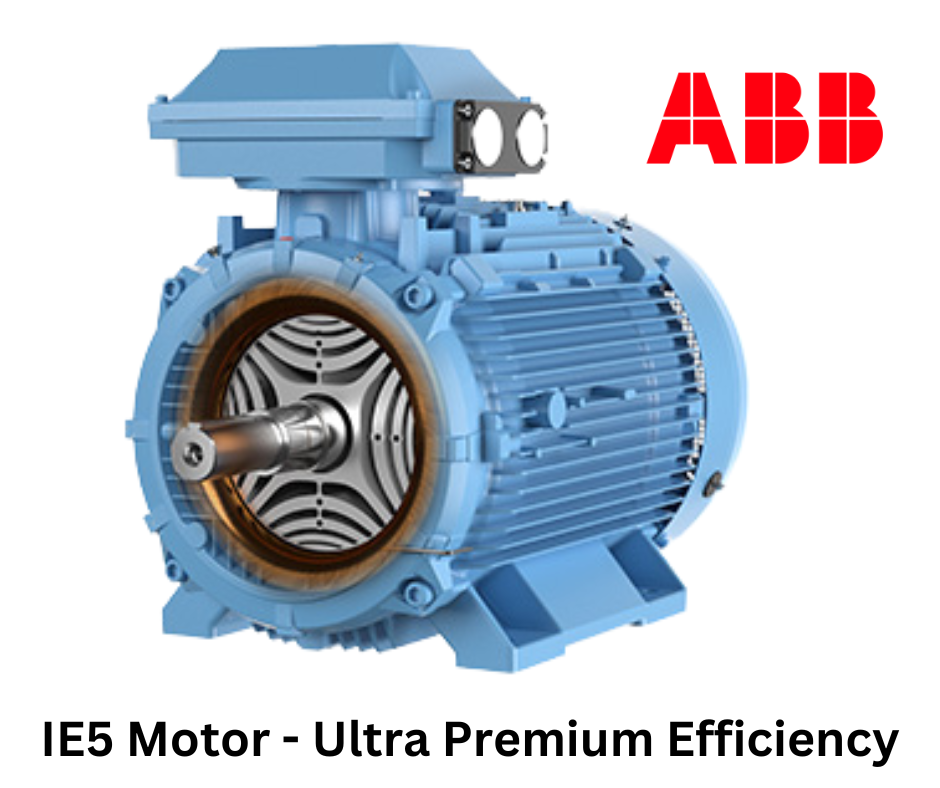
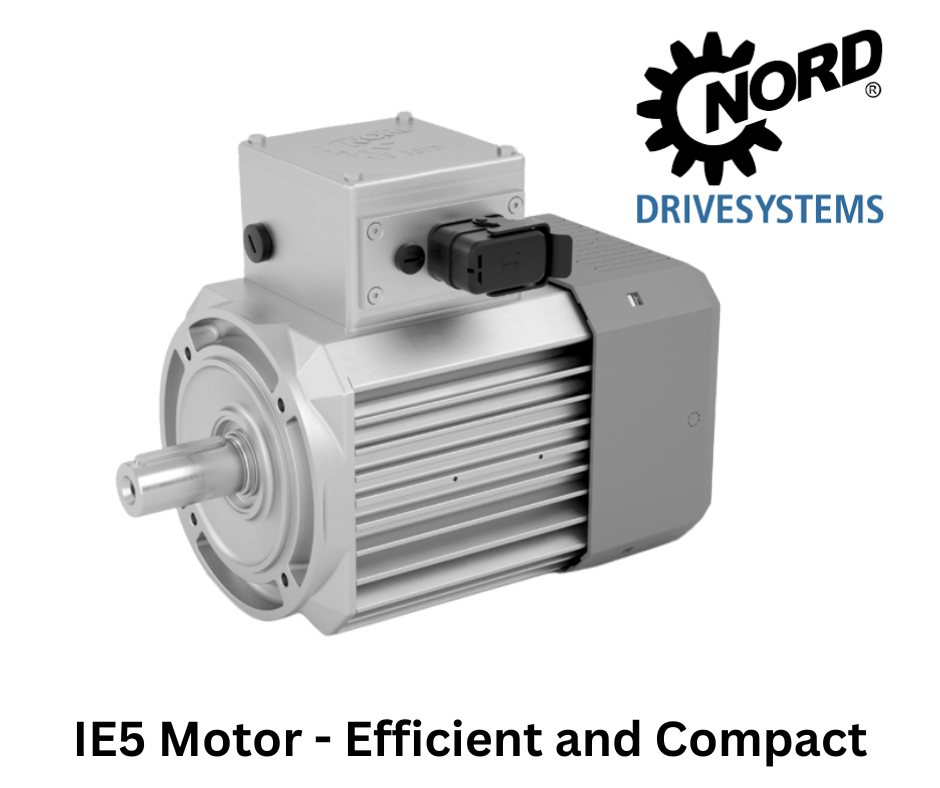
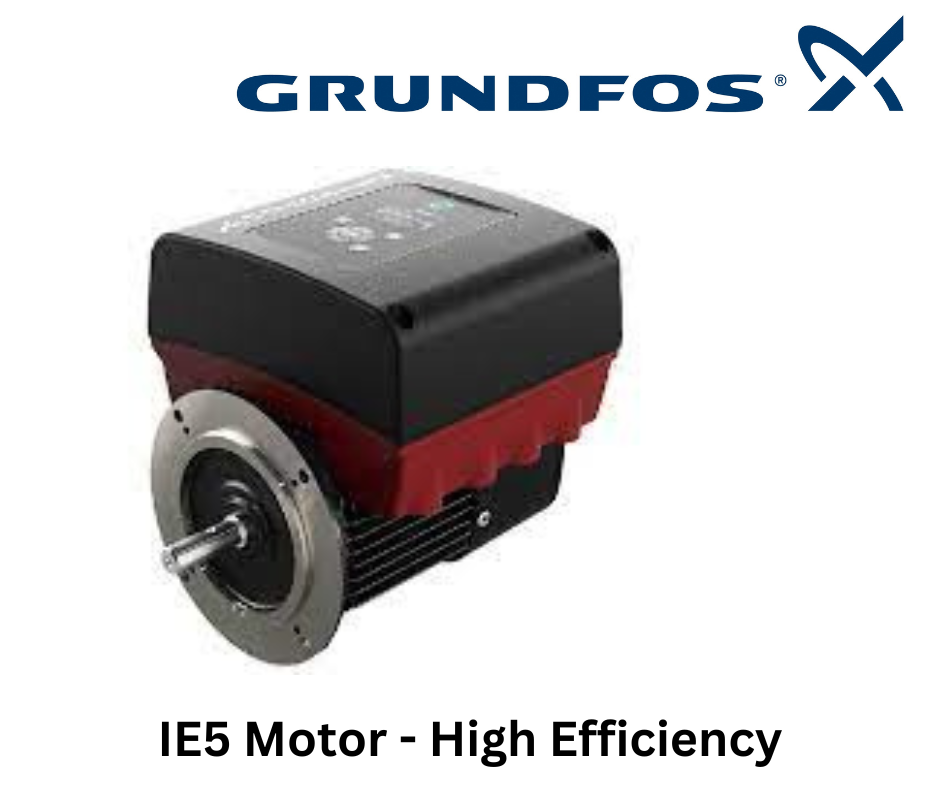
Integrated intelligence
Motors are also available with integrated intelligence to control energy use. The Flygt Concertor is a wastewater pump that incorporates an IE4 equivalent motor with a control system that automatically adapts to the changing environment.
The pump uses data, such as viscosity and flow, based on feedback from an initial period of cycles, enabling the Concertor to deliver the optimal pumping level according to conditions at the most efficient rate.
Improving your sustainability credentials
Increasing energy efficiency also contributes to your organisation’s environmental sustainability commitments. Demonstrating sustainability credentials might already be a request from your customers, and this requirement is set to become increasingly important in future. A reduction in energy consumption also provides a positive message your company can promote through marketing.
To find out more about a motor energy cost audit and whether integrating energy saving technologies can provide a pay-back for your organisation, talk to a Rotamec engineer.