Maintaining your servo motors for long-term performance
When using servo motors, the commonality with most applications is the need for high accuracy control. As soon as maintenance issues start to develop, this can quickly impact performance, negatively affecting the quality or productivity of the machine’s output. And, if maintenance requirements aren’t identified early enough, they can cause knock-on problems, escalating the issue with the potential to cause long-term harm to the motor. This will also increase downtime while any damage is rectified.
In this article, we’ll investigate the most common maintenance challenges that servo motors face. We’ll look at how to identify these problems, how to resolve them, and we’ll discuss how to avoid them in the first place.
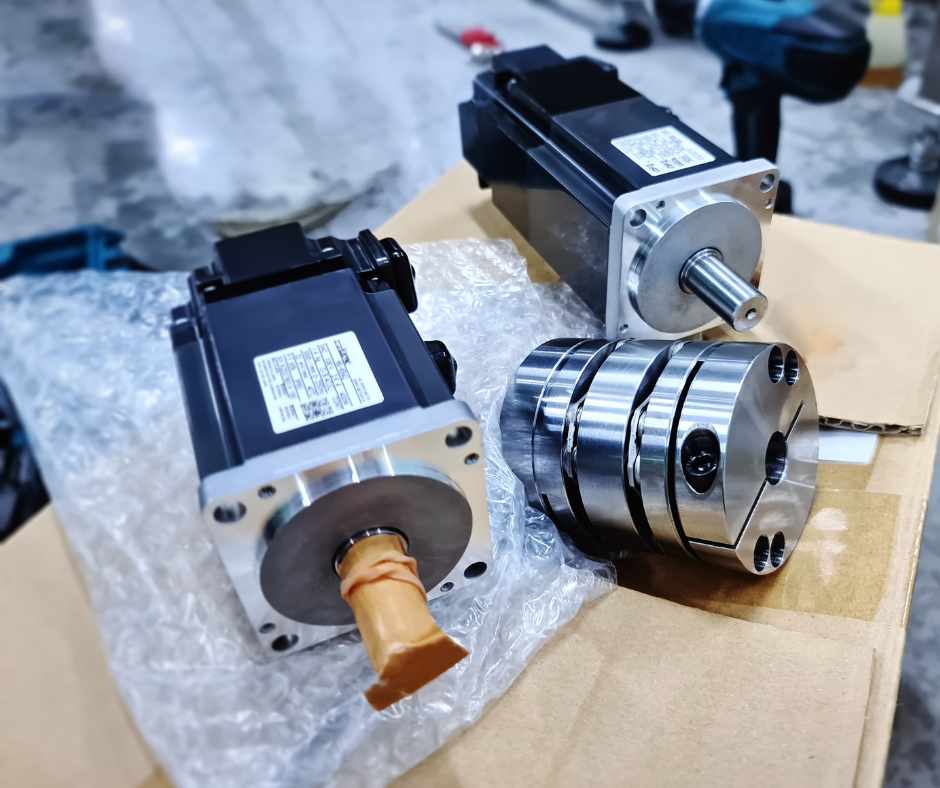
Bearing Failure
The most common problem facing servo motors is usually bearing deterioration. Damage to the bearings and bearing race will introduce friction, impeding motion control precision, that will reduce machine performance. If not quickly identified, bearing failure is also likely to cause further problems, such as throwing the encoder out of alignment, as well as overheating – challenges we’ll explore later on.
Bearing failure can result from various factors but is commonly caused by vibration, friction, and excessive heat, as well as general deterioration over time. A lack of lubrication, or low lubrication quality, as well as misalignment between the motor shaft and coupling, can also cause bearing problems.
Bearing deterioration usually presents with an audible warning. A servo motor typically operates with a high-pitched noise, so a change in pitch or a ‘grumbling’ can signify a problem. Excessive vibration can also mean bearing failure. If the encoder is out of alignment with the machine presenting an error notification, this too can be a result of a bearing problem.
If bearing deterioration isn’t noticed soon enough, this can develop into more significant problems. If the motor continues to run until the bearing has completely failed, the rotors and their magnets can hit the windings or core, which can create significant damage or at the very least, knock them out of alignment.
At its extreme, bearing failure exacerbated by high temperature and lubrication breakdown can in effect weld the bearings solid. With the momentum of the turning motor, this will spin the outer race, requiring complete disassembly and machining of a sleeve to prevent the bearing housing rotating along with the shaft.
Many servo motors are sealed units, but some servo motors have lubrication ports. In this case, regular greasing should be combined with checking the condition of the lubricant to ensure that it’s not hardened or burnt. To repair a servo motor bearing, we dismantle the motor and give it a thorough clean to enable detailed inspection of the complete bearing unit.
Repair to the races might be required if serious blemishes have developed, and typically we replace the bearings themselves. Dependent on the manufacturer, standard bearings aren’t usually as long-lasting or as efficient as aftermarket bearings from manufacturers such as NTN or SKF. Premium bearings will immediately give the servo motor a longer life, and depending on the application requirements, we can specify bearings for high speed or high loads that can more effectively deal with the friction and torque requirements.
Encoder fault
The servo motor’s encoder, required to provide closed-loop feedback on motor shaft position, operates with a magnet or, more commonly for widespread servo applications, an optical sensor. Optical encoders feature a glass disc with positional markings and a light beam that senses position.
Vibration, typically caused by bearing failure, can shift the position of the light beam, creating an inaccurate reading. This will impact accuracy of servo shaft position, or the control device will return an ‘error’ reading. While realignment of the encoder is required, it’s necessary to resolve the initial cause of vibration.
A challenge with optical encoders, compared to magnetic sensors, is that they depend on sensing the light beam, but this can be impaired with the accumulation of dust, meaning that the encoder loses position. This requires a careful clean of the glass disc, so it’s preferable at outset to protect the encoder from ingress.
The glass disc is also extremely fragile, and impact can easily shatter it, so it’s important to treat it with extreme care. Even when repairing an encoder, because of the sensitivity required for precise positional feedback, there’s always a risk involved in maintenance so it’s vital to partner with a workshop experienced in servo technology.
Rotor damage
Vibration can also be caused by damage to the rotor. If the weights used to balance the rotor become detached, which could happen over time in combination with excess heat, vibration can occur. The level of vibration depends on the motor speed, but 1g difference at 5,000rpm can be significant, impeding smooth operation. Resolving vibration caused through an imbalanced rotor requires a balancing machine to re-establish an equal weight distribution through precise addition of weight.
Despite the robust feel of a servo motor, they need to be handled with care as the magnets within the rotor are susceptible to damage. A cracked magnet will cause the servo motor to run with an unsteady rotation or fluctuating speed. In the worst case, it can cause a complete motor lock up.
Early identification, typically through vibration or temperature increase, is important, and the remedy is usually replacement of the magnets. Handling a motor during installation and maintenance should also be exercised with care.
Overheating
Overheating of a servo motor can cause a break down in the insulation between the core and copper windings, resulting in an earth fault. When the problem reaches this stage, temperature increase is accelerated and can lead to a chain reaction of problems such as damage to the motor’s magnets, bearing failure, or an encoder fault.
Overheating can be caused by an imbalance between too high a frequency and too low a voltage, so the correct input is vital. Considering their compact nature, servo motors don’t have a great deal of surface area from which heat can escape, so maximising airflow around them is usually needed. Similarly, it’s important to keep them clean, as a build-up of debris can trap heat. Maintenance problems with the machine mechanism that the motor is driving can also cause an overload on the servo that can develop into overheating.
Overheating can be detected with a sensor or simple manual inspection, taking care to maintain personal safety. Like many servo motor maintenance challenges, the remedy for overheating depends on the cause, from overload to bearing problems. It’s important to identify overheating quickly because the resulting damage, even when repaired, can mean that the motor is more likely to overheat again in future.
Servo motor fault diagnosis
Usually, when a servo motor suffers a fault, maintenance typically takes place in our workshop, where we have full facilities for inspection, repair, and testing. As we’re looking at the servo motor in isolation from its application, it’s important to gain as much information as possible about what the servo motor is driving. This useful data enables us to ascertain the fault a lot quicker, reducing downtime and cost for the customer.
Depending on the application, it can be useful to observe servo motor operation in situ. Under workshop testing, the servo might be running perfectly but re-installed with its host machine and subjected to the forces specific to the application can impact operation.
Particularly because of the usual high speed operation of servo motors, if maintenance issues aren’t quickly identified, more serious problems can develop, increasing damage to the motor and even to the machine itself. The cost of repair and replacement will also be exacerbated by productivity downtime. However, preventing servo motor problems can be achieved with a regular and comprehensive maintenance schedule, including thorough inspection to ensure that any emerging problems are identified at the first opportunity.